Practical Hydroponics
Issue 108: Intelligent Farm Management – Ghost Gully Produce
September/October 2009
By Steven Carruthers
Water restrictions and farm management issues have driven many growers to water-saving technology to ensure their operations are resource and cost effective. Ghost Gully Produce is an example of this technology playing a key role in intelligent farm management.
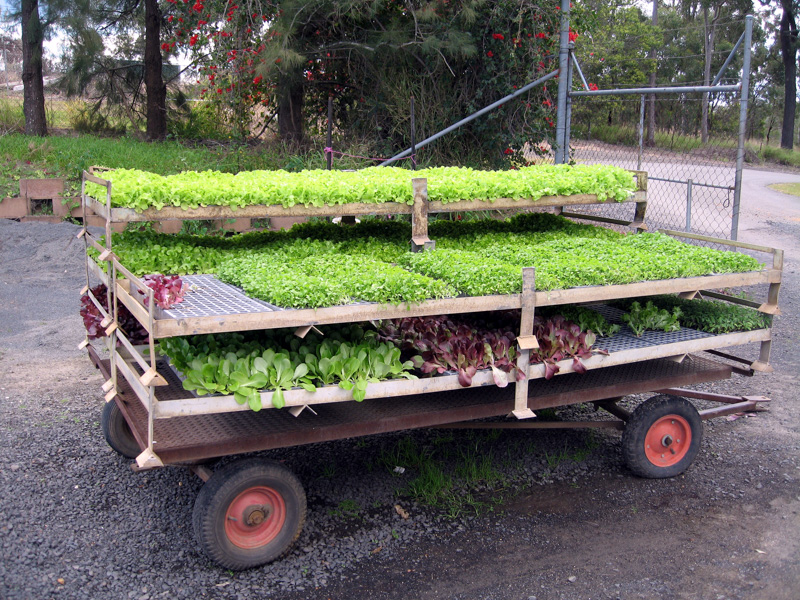
Ghost Gully grow seven lettuce varieties – red and green corals, oaks, minuettes and baby cos.
Farm infrastructure includes sand filters and a mist cooling system.
Gary and Kym Samuelsen.
Located in Gatton, Ghost Gully Produce is one of a handful of small family-owned hydroponic farms in the Lockyer Valley, in South East Queensland. Gary Samuelsen, a former dairy farmer, turned to hydroponic lettuce and herb production not long after the dairy industry deregulated. Seven years ago the family purchased a run-down 18 ha nursery, mostly scrub, with four small greenhouse structures (20m wide x 75m long). Gary replaced the plastic roofing with hail net and adapted the existing benching infrastructure to an NFT growing system using half-round stormwater pipes with soft plastic covers and slits to accommodate seedling plugs.

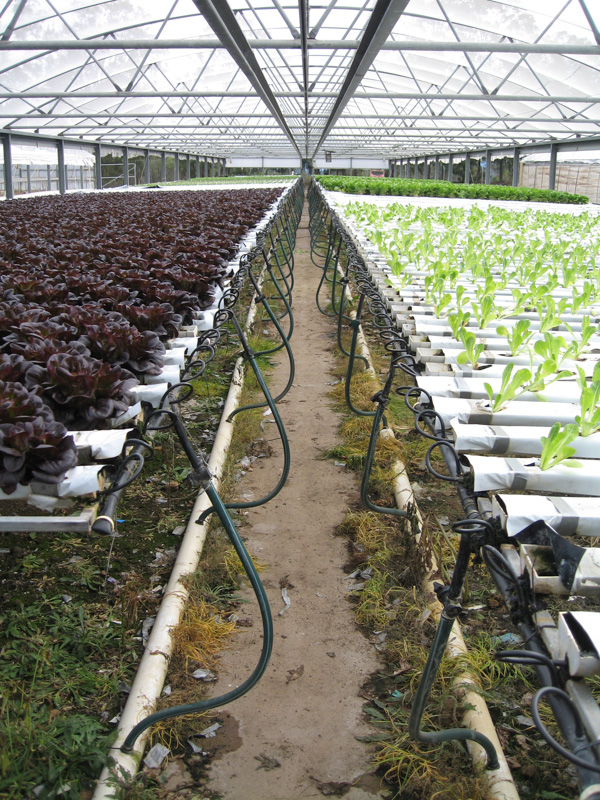
“That got us started,” said Gary, “and then we met Joe who formulated our nutrient and introduced us to proper channel with clip-on lids.”
Joe Crane is a specialist consultant in the region with over a decade of experience in nutrient formulation, hydroponic system analyses and design, and farm automation, including cold room temperature logging. The collaboration has resulted in new farm infrastructure, including washing, packing and cooling sheds, five new NFT growing systems under 1 ha of hail net, Black Max ozone water disinfection equipment, and a WiSA water management system.
Water Management System
The Australian-developed WiSA system was primarily designed as an irrigation system for field farming to enable precise control of water and nutrient applications. The system is connected to a dedicated PC 24/7 to get the optimum data and utilisation of equipment. Following a number of below average rainfall years and severe water restrictions in South East Queensland, Joe took it upon himself to redesign the system for hydroponics. WiSA was so impressed the Victorian-based company appointed Joe its Queensland distributor, and Ghost Gully Produce became the first hydroponic farm to adopt WiSA water-saving technology.
“Stage 4 water restrictions meant we had to reduce water usage by 25%,” explained Joe. “The WiSA system allowed us to attain 33.3% water saving,” he added.
When Gary first started the business he used town water but was beset with problems including Pythium and occasionally over-chlorination. Today, he uses a combination of town and dam water and ozone disinfection.
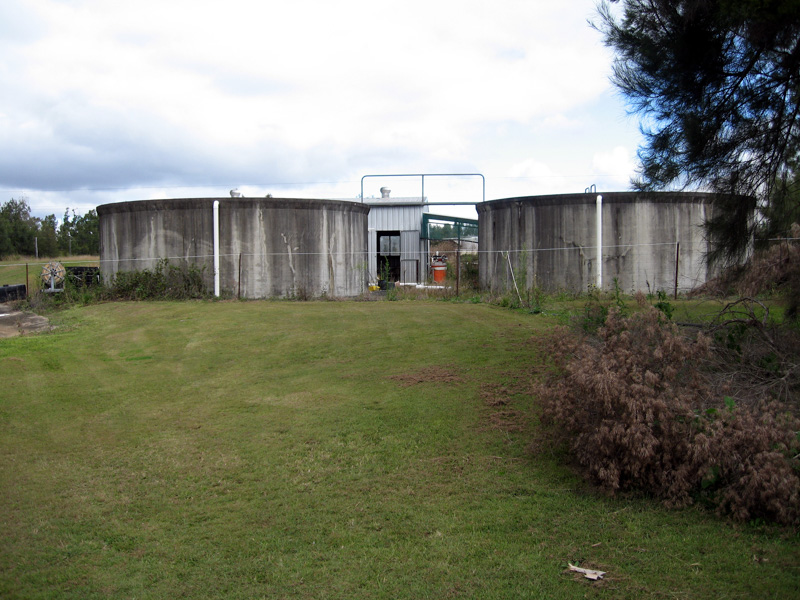
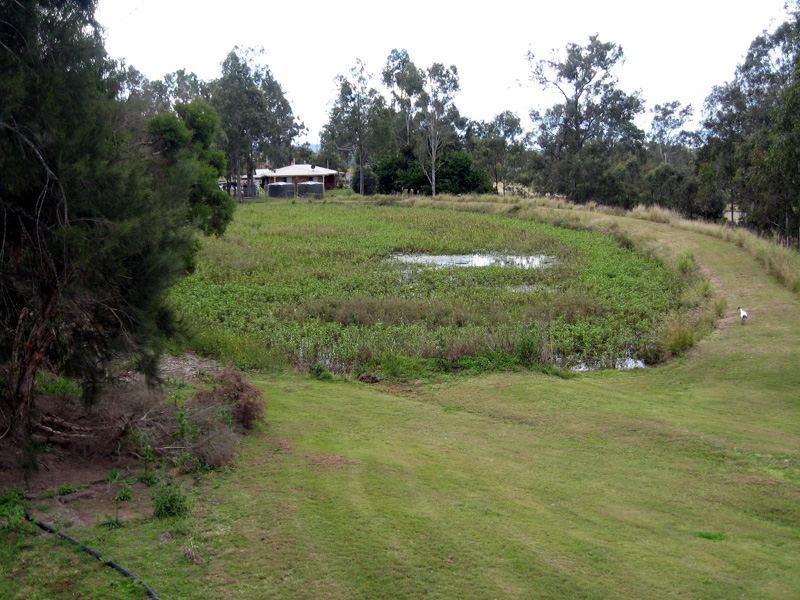
From the dam, the catchment water is pumped into three large storage tanks (95,000L each) where it is treated with Sporekill to reduce the pathogen load. When required, the water is transferred to duplicate upper level storage tanks with in-line ozone (O3) injection to ensure the water is free of pathogens. The upper storage tanks supply clean water pumped to eight growing systems on the property.

Each growing system has its own dedicated reservoir tank (10,000L), dosing equipment and ozone generator. In total, the farm operates 14 Black Max ozone generators at strategic points throughout the water system to prevent water-borne diseases.
The WiSA system works in real-time, that is, what is happening now, not last week. Variable factors such as water usage, farm tank levels, system pressures, nutrient conductivity, pH, temperature (air and water), humidity, rainfall, nutrient dosing times and valve timing are monitored and logged by the WiSA system.
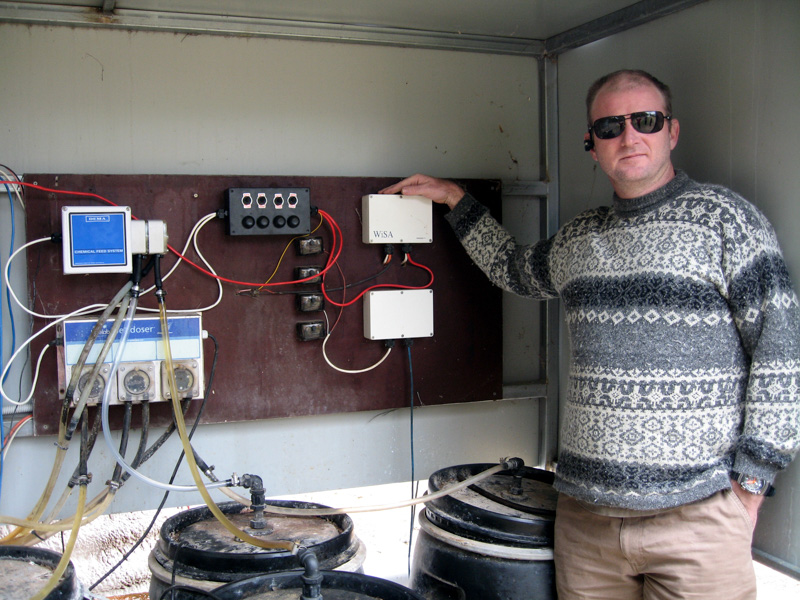
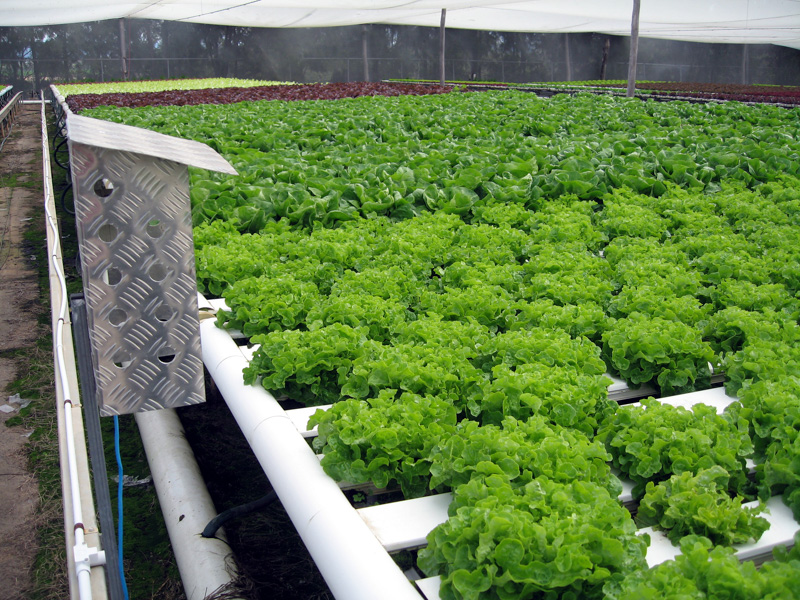
“These variables are the basis for automated decision-making on the farm, and can be graphed and recalled individually and comparatively over time periods for farm management decisions,” explains Joe.
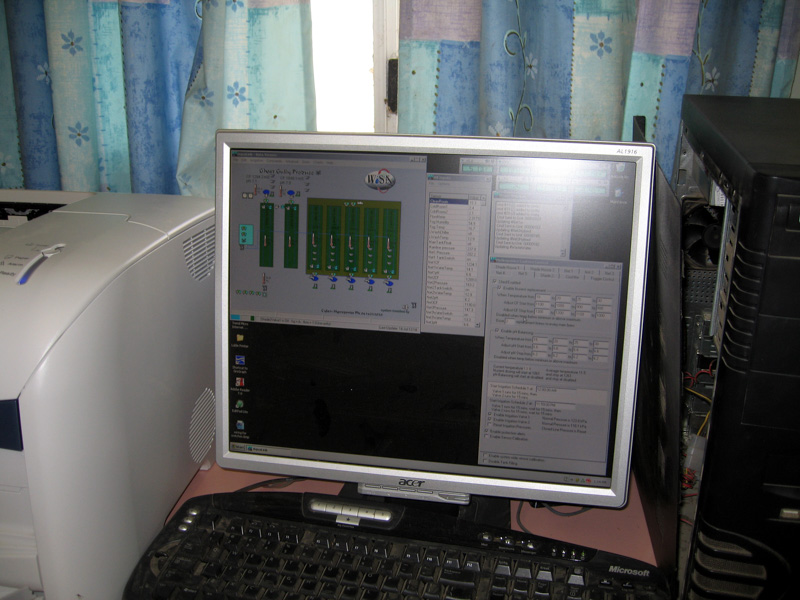
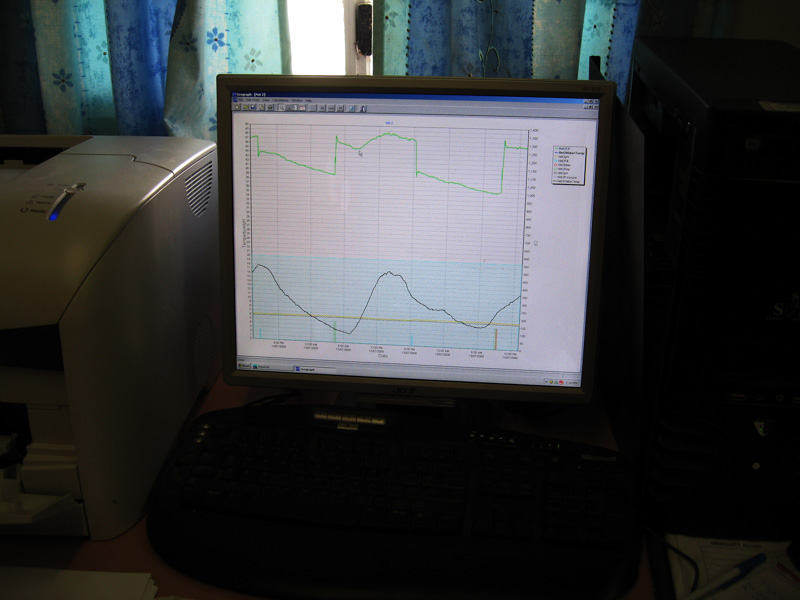
The level of monitoring also extends to the washing shed and cold-room where sensors record temperature in 30-second increments.
“In the event of a dispute over cold-chain management, we’ve got the records,” said Joe.
An interesting aspect of the WiSA management system is nutrient management. By analysing the conductivity factor and water temperature of the nutrient reservoir, the conductivity can be adjusted according to water temperature on a floating scale. Nutrient is added to increase CF via automated dosing pumps, and CF is decreased through plant usage.
“The computer scales the nutrient formulation for us,” explains Joe. “Most of the time we run so long that we only dump when it rains,” he added.
The farm’s nutrient formulation process is proprietary to Joe’s consultancy business, Cyber-Hydroponics, with nutrient formulations uniquely tailored to suit water supply, individual crops, and to account for seasonal variations in temperature. Farm formulations are prepared by the farmer, offering a cost saving over conventional nutrients.
Ozonation
At first, the use of multiple Black Max ozone generators (BM2s) at different points in the water system seems excessive.
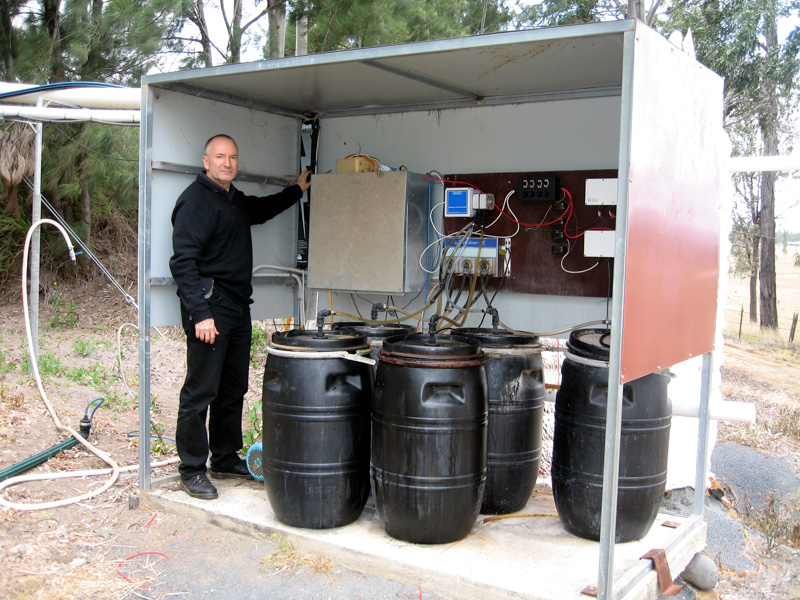
“The farm is spread over a large area and it was more practical to use multiple units,” explains Gary Davies, principal of Adelaide-based Black Max Ozone Generators. “A smaller, centralised farm would not require as many units” he said.
The Australian-made Black Max ozone generator was first introduced to the hydroponics industry in the late 1990s, at a time when many growers were unaware of the benefits of using ozone, or O3, to disinfect water. It is one of the most effective bactericides known to science. On the oxidation chart it is listed above chlorine, iodine and bromine, but unlike these chemical options for disinfection, ozone dissolved in water breaks down to oxygen in 15-20 minutes, leaving no chemical residues.
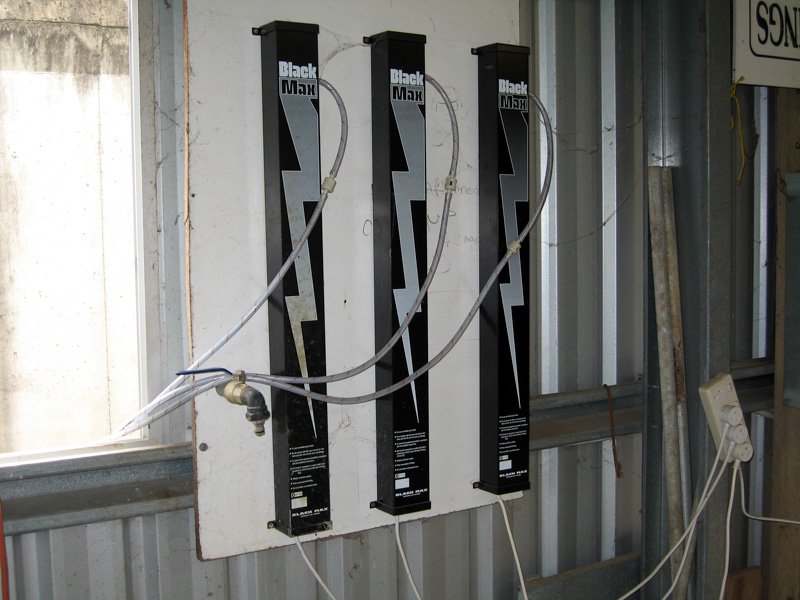
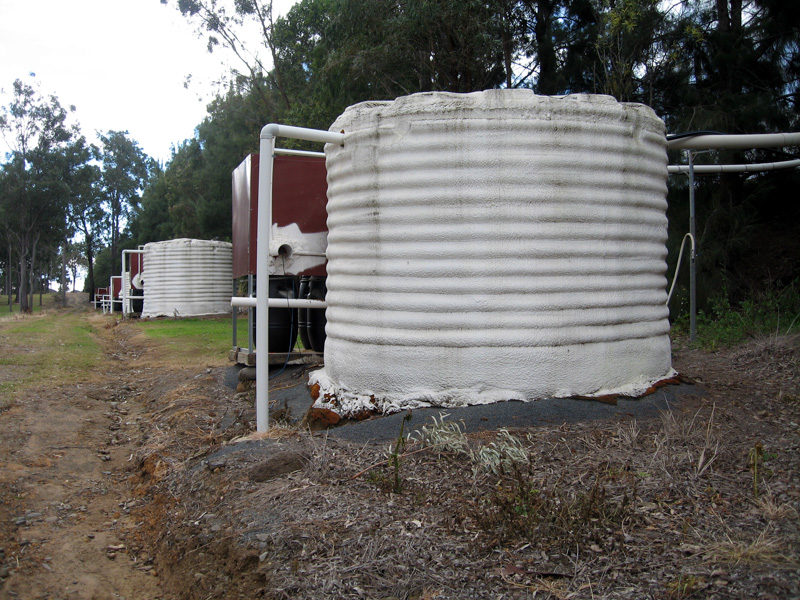
Ghost Gully uses the BM2 unit, which produces 2.6mg of ozone/litre of air for treatment of reservoirs up to 10,000 litres. Black Max also makes the smaller BM1 that produces 0.6mg of ozone/litre of air, for treatment of any size reservoirs up to 2,000 litres. Housed in marine grade aluminium casings, the BM1 and BM2 use a high quality ozone-producing UV lamp operating at a precise wavelength. The units have a small see-through window to easily and quickly check lamp operation. Ozone is introduced in-line using the ‘venturi’ principle, a vacuum effect caused by a reduction in fluid pressure that results when a fluid flows through a constricted section of pipe.
Both the grower and Joe are convinced about the effectiveness of ozone. Joe recalls an incident when an ozone lamp failed and a pathogen problem became evident in one section of the farm.
“Gary called me the next day about a problem on the farm, something we hadn’t seen for a long time,” recounts Joe. “We quickly worked out that an ozone lamp had failed after several years’ use. We put a spare unit onto the system and the problem quickly disappeared.
“There is no doubt in our minds about the effectiveness of the ozone system in pathogen control.”
Ozone is also used in the washing water to remove bacteria, fungi and moulds, and is said to extend the shelf-life of produce. Trials at Ghost Gully Produce point to a 3-week shelf life once lettuce leaves the cold-room.
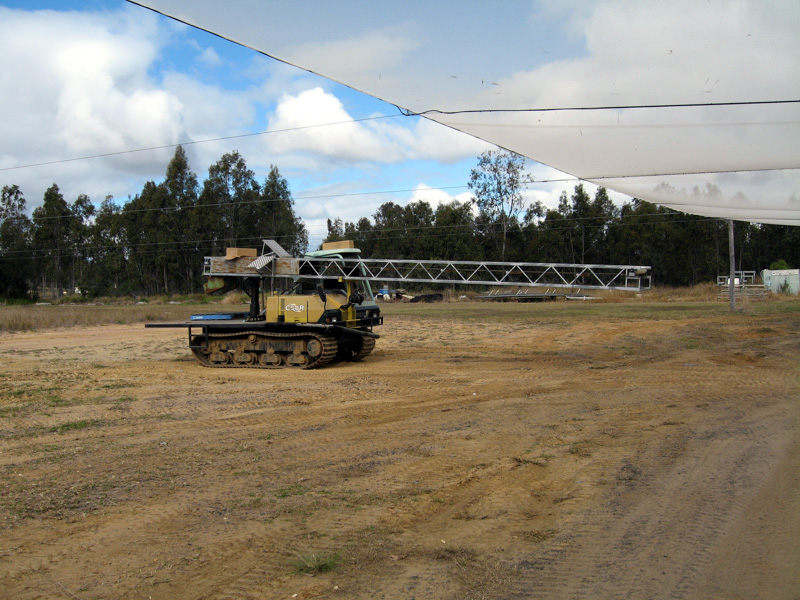
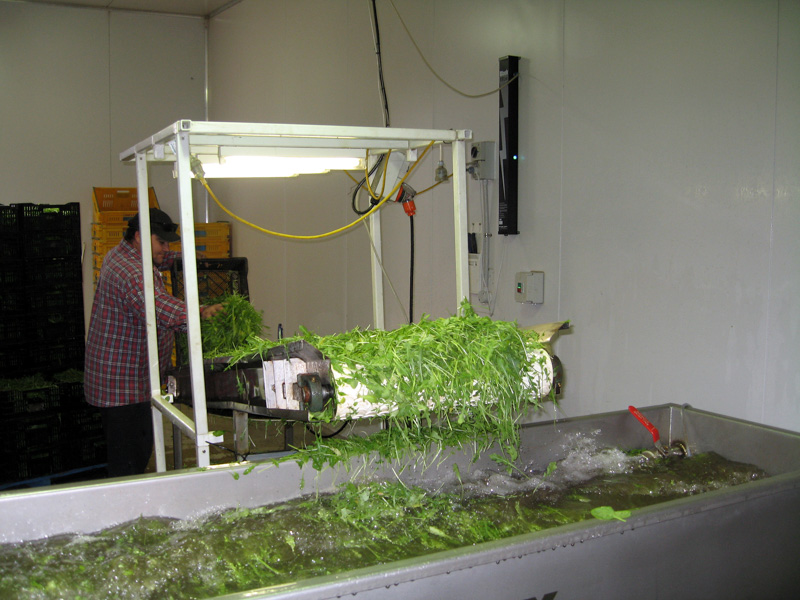
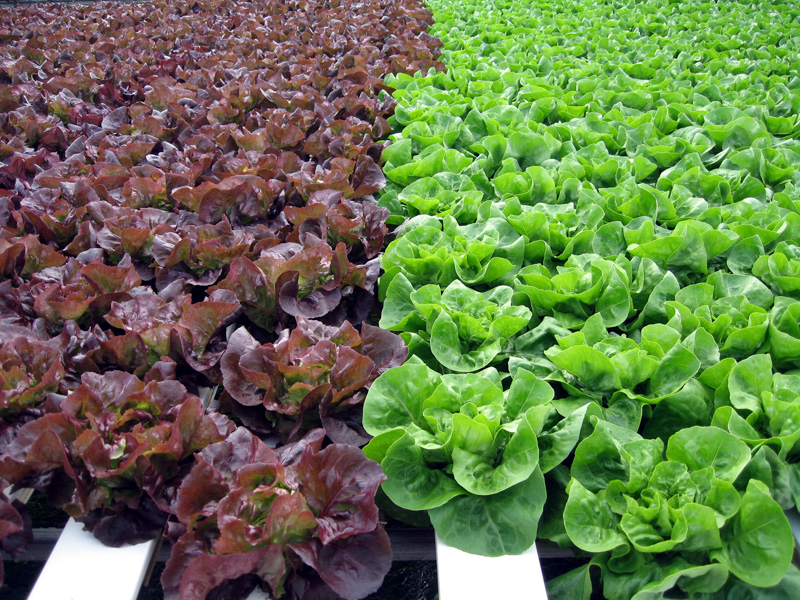
“They just last longer,” said Gary Samuelsen.
The longer shelf-life could also be partly attributed to a twice-weekly foliar spray of SilikaMajic, a potassium silicate-based product from Flairform (www.flairform.com.au).
“It’s got to be a good thing,” said the grower. “It promotes cell growth and slows down transpiration. In summer, lettuce stay good for an extra 2 days, longer than normal without it,” he added.
According to Joe, ozone is extremely effective at controlling water borne diseases such as Pythium.
“Pathogens are always there,” he explains, “but ozone keeps them under control.”
He added that pathogens are hardy and likely to harbour in irrigation lines.
“Most are eliminated when the return water reaches the system reservoir, which is ozonated 24/7,” he said.
“I recommend that all my consulting farms use the ozone sterilisation method. As well as being effective, the Black Max units are robust and have an excellent life.”
At under $1,000, the Black Max ozone generators are supplied with a fully assembled installation kit consisting of 3 metres of ozone hose, non-return valve and ozone jet (venturi). Accessories include a ‘maxizone’ injector that requires a minimum flow rate of 1,800 litres/hr and a ‘megazone’ injector manifold requiring a minimum flow rate of 9,000 litres/hr, to suit 1-2 hp pumps.
Final remarks
With an annual production capacity of over a million plants and plenty of room to expand, Ghost Gully continues to be a work in progress.
Water-saving practices start at the dam, which has been allowed to grow over with weed to minimise evaporation. It also eliminated the large duck population that once frequented the dam.
“If ducks can’t see the water, they won’t land,” quips the grower.
On-farm water-saving practices also include capturing overflow rainwater, referred to by the grower as “God’s nectar”, from the building structures and growing systems. All the system tanks have overflows that route excess water to a lower catchment tank (38,000L). When the water reaches a certain level it is pumped to the upper storage tanks.
But the heart of the operation is the WiSA water management system that allows produce to be turned over from seedling to market in a way that’s both resource and cost-effective. Recording variables such as water usage and storage and processing temperatures assists with the farm’s water efficiency program and Quality Assurance compliance.
Ghost Gully has shown that ozone disinfection is simple and efficient, with benefits including higher yields and quality and longer shelf-life, and no chemical residues. Where ozone disinfection was once cost-prohibitive for many small and larger growers alike, the Black Max ozone systems are affordable.
Ghost Gully Produce is a highly successful operation and a prime example of automation playing a key role in intelligent farm management.
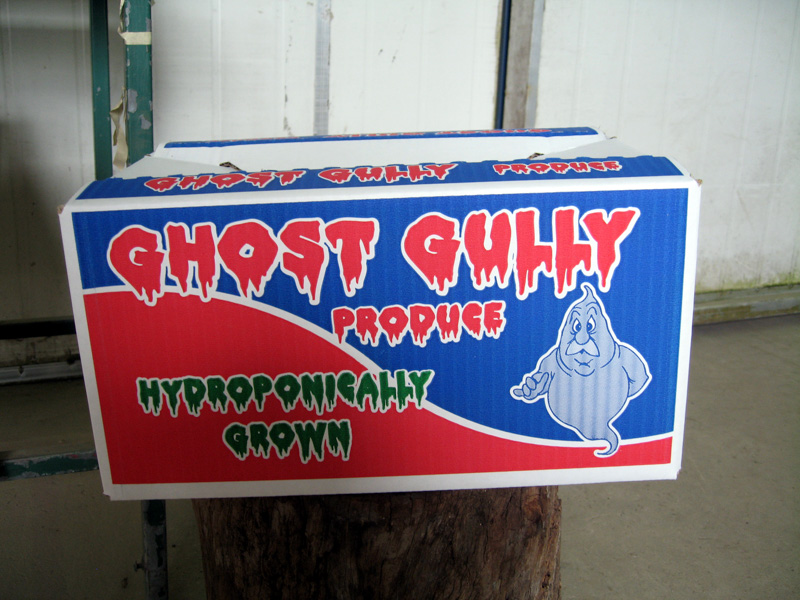
Article and photos by Steven Carruthers
Extracted from the Practical Hydroponics & Greenhouses magazine issue 108